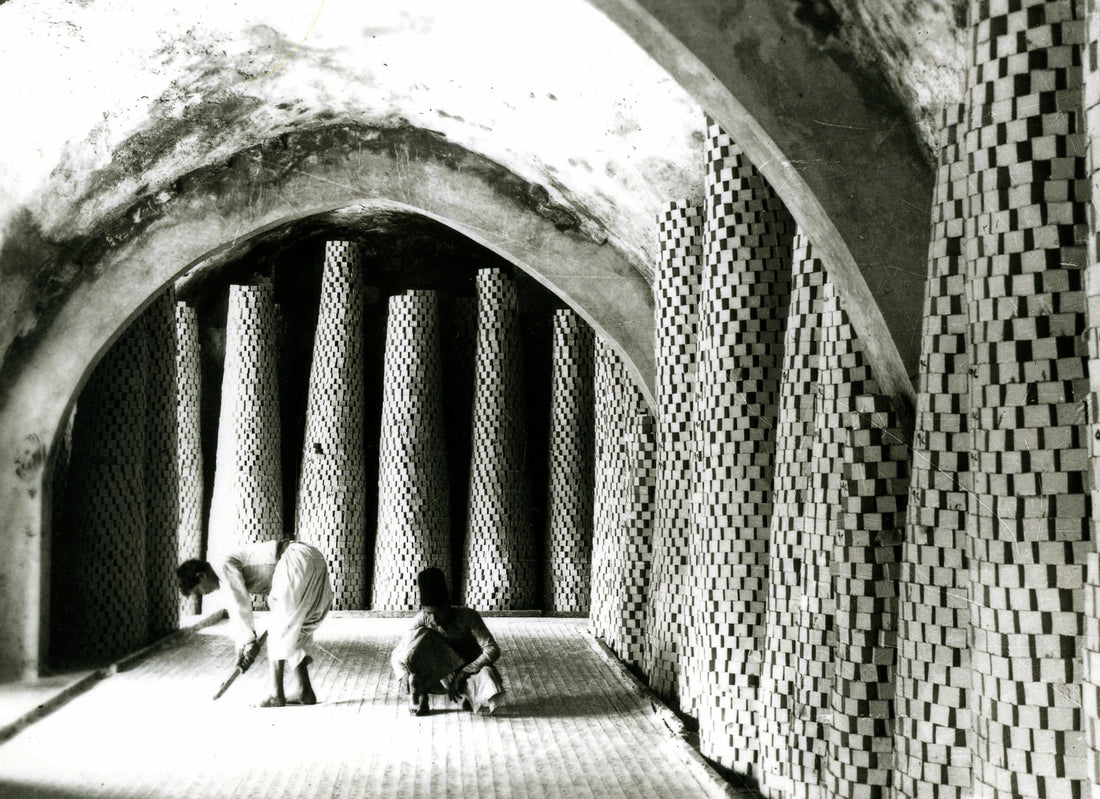
Soap Making in Palestine
Share
Table of Contents
1. History
The history of soap-making in Palestine spans over a thousand years, as demonstrated by accounts from ancient travelers and historians. Among these is Shams al-Din Muhammad bin Abi Talib al-Ansari, also known as "al-Maqdisi," who lived during the 13th century AD. In 1200, during his visit to the city, he noted how much soap was produced there and exported abroad. He also praised Nablus's bountiful environment, writing: "This city represents a palace amidst orchards, divinely blessed with the olive tree."
The exact origins of the soap industry, its inventor, or whether it was developed in Nablus or culturally diffused from another city, remain unclear. The first archaeologically recorded soap date to ancient Iraq around 4500 years ago, calling for a recipe similar to what is used in today's Nabulsi soap (oil, water, and salty alkaline powder). What is certain is by around a thousand years ago Nablus provided a suitable environment and the propitious conditions that allowed the industry to flourish more than elsewhere. One of the primary reasons for this was the abundance of olive oil in and around Nablus, as the oil is the main ingredient in Nablusi soap-making. Historical records indicate that at the time Nablus olive oil was sent to places such as Damascus for use in the Umayyad Mosque and was also exported to numerous countries and islands in the Mediterranean Sea.
During the European Crusaders' occupation of Palestine, Nablus gained prominence for its production of exceptional soap, which was highly regarded for its quality. The soap-making industry became a royal monopoly, with the King overseeing it. Factory owners were granted the right to practice the craft under a contract with the King of "Jerusalem" in exchange for regular financial contributions. This arrangement ensured that the soap-making industry remained under the control of the elite.
The Crusaders sought to expand their influence by transferring the soap-making craft to Europe. As a result, soap factories utilizing olive oil pomace were established in Marseille, France. These European factories adopted and adapted the methods used in the creation of Nablusi soap, thus preserving and spreading the techniques that originated in Palestine.
During the Ottoman era, the soap-making industry further evolved into an exclusive domain reserved for wealthy and influential individuals due to the substantial revenue it generated. The practice of soap-making became a closely guarded family tradition, limited to a select group of families who became closely associated with the craft. The intergenerational transfer of knowledge and skills within these families ensured that the unique techniques of soap-making continued to thrive and develop throughout the region.
At the beginning of the twentieth century, Egyptians and Syrians took note of the soap-making industry's popularity and began producing soap under the name "Nablusi soap." Despite this, the authentic Nablusi soap continued to represent quality and garner attention.
Until the late 19th century, Nablus boasted 30 soap factories. However, these factories gradually dwindled in number until only 16 remained in 1904, with an annual production of 500 to 1,000 tons.
On the eve of World War I, the number of soap factories in Nablus experienced a resurgence, totaling 29—including 23 large factories and 6 smaller ones. These factories produced between 2,400 and 2,640 tons of soap.
In 1930, the once thriving soap industry in Nablus experienced a sharp decline. This downturn was brought on by several factors that negatively impacted the industry. Firstly, there was an inability to protect the brand name, which led many commercial factory owners to imitate the reputable soap brand. This created confusion in the market and diluted the value of the original Nablusi soap.
Additionally, the Egyptian government, in cooperation with the British Mandate government, imposed customs taxes on the soap, making it more expensive and less competitive in the market. At the same time, the Syrian government levied consumption fees on Nablusi soap, further increasing its cost and reducing its appeal to consumers.
Lastly, the British Mandate authorities permitted the import of foreign soap, which competed directly with the local soap industry. They also encouraged Jewish immigrants to establish soap factories that used cheap vegetable and animal oils and fats as raw materials. This influx of lower-cost, alternative soap products further weakened the Nablusi soap industry, contributing to its decline in 1930.
After 1967, when the remaining Palestinian territories, including the city of Nablus, fell under Israeli occupation, the occupation authorities sought to destroy the Palestinian economy, targeting the soap industry, like other Palestinian national industries. Soap factories gradually disappeared as the local market was flooded with various types of foreign and Israeli-made soap at relatively low prices.
During the Al-Aqsa Intifada, soap factories were directly targeted by Israeli occupation missiles and tank shells, destroying three of them in the Al-Yasmine neighborhood and causing significant damage to several others.
According to figures from the Nablus Chamber of Commerce and Industry, the number of officially registered soap factories by the end of 2021 was 9, with 6 in the city and 3 in the surrounding villages.
In 2012, there were only 4 soap factories, and the figures indicated that the value of Nablusi soap exports that year reached $1,736,496. The source also noted that the largest Arab importers of Nablusi soap were Jordan, the United Arab Emirates, and Iraq, while some foreign countries importing Nablusi soap included Japan, Korea, and Peru.
Due to the closure of many soap factories in recent years and the reduction in production by many others, competition from industrial soap has increased.
2. Materials used in soap making:
- Olive oil at approximately 82%.
- Sodium hydroxide at approximately 13%.
- Water and other materials at approximately 5%.
3. Tools used in soap making:
The Nablusi soap industry does not involve complex machines; rather, it is a manual process that relies on workers. The main tools used are:
- The Pot (القدر - Al-Qidr): A concave, circular copper piece with a diameter of approximately two meters and a thickness of up to 2.5 cm. It is placed at a depth of two meters or more and surrounded by a thick firestone wall connected to the copper base, which is polished from the inside. A thick wooden ring rests on the upper edge of the pot. The pot can hold about 250 jars of oil, equivalent to over 5 tons, in addition to other materials used in soap making.
- The Mixer (المركب - Al-Murakkab): A wooden rod measuring roughly two and a half meters in length with a 25 cm diameter wooden disk attached at the lower end. The mixer is used for stirring at the beginning of the saponification process.
- The Stirrer (المقلد - Al-Muqallid): Resembling a paddle, this wooden column is about 4 meters long and 7 cm in diameter, with a circular wooden piece at the lower end. It is used to stir the mixture during the saponification process.
- The Sampler (المثقب - Al-Muthqab): A wooden tool used to take soap samples for examination by the supervisor. It resembles the sign () with a long tip of about 25 cm.
- The Floater (العوامة - Al-'Uwama): Two wooden rods, each 3 meters long, connected at one end with a rectangular piece of wood and tied with a rope at the upper end. The floater is used at the end of the process to collect the soap at the bottom of the pot above the water level.
- The Spreading Box (صندوق الانتشار - Sanduq al-Intishar): A round tin container with a thick wooden base, accommodating approximately 17 kg of viscous (gel-like) soap.
- The Fork (الشوكة - Al-Shawka): A flat iron piece with a pointed end and a wooden handle, its length equal to the depth of the soap during spreading. It is used to determine the thickness of the soap during the spreading process.
- The Leveling Tool (أداة التسوية - Adat al-Taswiyah): A flat iron piece with a wooden handle, used to level the soap surface after the spreading process.
- The Scraper (المكشطة - Al-Mikshata): A curved sheet with a wide-angle and wooden handle, resembling a razor blade.
- The Cutter (Knife) (المقص - Al-Muqass): A special knife attached to a 70 cm long wooden arm.
- The Twine (الخيط - Al-Khayt): Linen thread coated with red iron earth chalk.
- The Compass (البوصلة - Al-Bawsala).
- The Stamps (الختم - Al-Khatim): A copper piece with the registered product mark, attached to a wooden hammer.
4. Stages of soap making:
The soap-making process goes through several main stages: cooking, spreading, marking, stamping, cutting, drying, and wrapping.
4.1. Cooking Process:
In the pot, alkali (القلوي, al-qalawi) is placed, which is a concentrated solution of caustic soda with a specific constant concentration and a known amount estimated to be one-third of the total cooking volume. Then, the fire is lit under the pot until the solution boils, and the oil is poured onto the solution in the pot (this process is called "oil return" or "رجوع الزيت", rajou' al-zayt). Nowadays, the oil return process remains enjoyable; the oil is transferred from the well by a special bucket to a jar, then to the pot, and the transfer process is accompanied by counting the number of transfers in a loud voice accompanied by chants, praise, and wise sayings; the count continues without boredom. The fire is then lit in the furnace (القمّم, al-qummem) under the pot, where the "sprayer" (the spray worker) or "راش" (rash) throws the cake onto the fire until the oil boils, expands, and rises in the pot. In the meantime, stirring is done using the paddle, and a little table salt is added to help increase the concentration of the soda solution in the pot.
Afterward, most of it separates and remains at the bottom of the pot. Then, a quantity of hot caustic soda solution is extracted from the designated spout and placed on top of the open-faced and perforated bottom barrel, which is positioned above a basin to collect the alkali, thus increasing the concentration of the alkali. The concentration is then measured using a special density meter to determine the amount of soda consumed.
Next, the workers lift the concentrated alkali from the basin using a bucket with a movable handle and sprinkle it over the oil in the pot, which is called a "return" (الرجعة, al-raj'a), and the head cook stirs it with a long wooden stick (دكشاب, dakshab). The process is repeated until approximately half of the required soda amount is added to the oil. After each return, the fire is ignited until the "insertion of the boil" (دخول الغلي, dukhoul al-ghali) occurs, meaning the mixture in the pot changes from one state to another; this indicates that the boiling process is complete for all the contents of the pot.
Increasing or decreasing the soda ratio causes defects in the soap; an increase in the ratio speeds up the soap's drying process, causes its edges to break when cut, and causes the soap to warp due to the excess soda coming out on the surface of the soap piece, which harms hands and clothes when used. A lack of soda, on the other hand, leads to a delay in soap drying, shrinkage of the surface of the piece upon complete drying, and an unpleasant oily smell that indicates poor-quality soap.
The final stage involves giving the soap a certain amount of water while stirring and boiling, which is called "rinsing" (الشطف, al-shataf). This process is necessary to provide the soap with a certain softness and to wash it from excess soda and impurities originally related to the oil. Here, some water remains in the soap and is separated by pouring an amount of alkali water. This process is called "dilution" (التخفيف, al-takhfeef). Then, the soap is stirred with the long wooden stick (دكشاب, dakshab) and boiled until the "insertion of the high" (دخول العالي, dukhoul al-'ali) occurs.
After that, it is left for a period ranging between 10 and 15 hours, allowing the excess water to separate and settle at the bottom, with the soap floating above the water in the pot because it has a lower density. This separation makes the soap ready for spreading. Once the soap reaches the desired consistency, it is carefully poured into molds or onto a flat surface to solidify. After the soap hardens, it is cut into individual bars or pieces and left to cure for several weeks. During this curing time, the soap continues to dry and harden, ultimately resulting in a high-quality, long-lasting product that is gentle on the skin and effective in cleaning.
4.2. Spreading Process:
The spreading process starts at dawn the day after the soap has been left to rest overnight. A worker fills a specialized bucket with the sticky, gelatinous soap and pours it into a spreading container. This step is repeated until the container is full. Another worker then carries the container on their shoulder and transports it to the lower floor, known as "the spreader," with the help of several colleagues.
4.3. Planning Process:
Once the soap has been spread out, it is left to dry for several hours in winter or a full day in summer. After drying, cutting workers manually smooth the soap's surface before determining the size of the soap pieces using a right angle and compass. A snap line is then immersed in a red solution called "ghamra" to create horizontal and vertical parallel lines.
4.4. Stamping Process:
The white surface of the soap displays red squares once it is spread out. A worker then stamps the center of the squares with a seal attached to a wooden mallet, showcasing the soap brand. One or two workers use individual seals to stamp each square. Impressively, a single worker can stamp 50,000 soap pieces within 90 minutes to two hours. This is done by holding two stamps in both hands and striking rhythmically (right hand strikes as the left hand lifts, and vice versa), all while quickly crouching and crawling.
4.5. Cutting Process:
Following the stamping process, the soap is cut by inserting a knife into the red lines and pulling it to complete the cut, both lengthwise and widthwise.
4.6. Drying Process:
The soap is left on the ground for one or two days before cutting workers lift it and arrange it in stacks called silos, each containing approximately 24 pieces. The soap is then organized into conical shapes over three meters high, called "tananeer," to facilitate drying. The soap dries for a month or more. Historically, the soap production season would start with the beginning of the oil season and continue until March at the latest. The soap would not be sold by the owner until July.
4.7. Wrapping Process:
Initially, soap was not wrapped. Wrapping began in the 1940s, with each piece being hand-wrapped in thin paper featuring the name and brand of the soap maker. A worker can wrap soap pieces at an average rate of 800 pieces per hour, while some can exceed 1,000 pieces. Annual competitions are held among wrapping workers.
Soap used to be placed in special boxes and transported to Egypt and the Levant by train. In the 1940s and early 1950s, soap was repackaged into small burlap bags (weights) weighing 10 kg, 15 kg, or 20 kg. Some mechanized developments were introduced at certain soap factories, such as electrically powered stirring instead of using wooden paddles and electric pumps for oil transfer from wells. Oil fuel sometimes replaced the traditional solid fuel called jift consisting of crushed olive pits and skins.
—
translated from Arabic and edited by the workers of the Palestinian Soap Cooperative Inc from the original article by the Palestinian News and Information Agency.